Micro 3D Printing Revolutionizing Precision Fashion Manufacturing in 2024
Micro 3D Printing Revolutionizing Precision Fashion Manufacturing in 2024 - Nanoscale Precision Empowers Intricate Textile Designs
The ability to work with materials at the nanoscale level is transforming textile design, particularly with the rise of micro 3D printing. This level of precision allows for the creation of highly complex and intricate patterns, textures, and even three-dimensional structures within fabrics, far surpassing what was possible with traditional textile methods. This newfound control isn't limited to aesthetics; it opens the door for integrating functional elements directly into the fabric's structure. We're now seeing examples of clothing with built-in temperature regulation or other advanced features woven into the very fabric of the garment. The possibilities for personalization are also expanding, as designers can manipulate the material at a level previously unimaginable, potentially leading to truly unique and customized clothing items. It is plausible that the combination of advanced 3D printing and nanoscale precision could eventually revolutionize the design and production of garments, shifting how we think about fashion in the years to come.
The ability to manipulate materials at the nanoscale is unlocking a new era of intricacy in textile design. We can now envision clothing with embedded microstructures that actively manage moisture, like intricate patterns designed to efficiently wick away sweat. Additionally, nanoscale 3D printing empowers the creation of garments with dynamic, adaptive properties. Imagine textiles that subtly morph in response to temperature fluctuations, or clothing that adjusts its structure based on wear and movement.
This newfound precision also allows for the integration of nanomaterials like nanofibers into textile structures, strengthening fabrics while maintaining fine detail. This has the potential to revolutionize the creation of delicate yet durable garments. Furthermore, the embedding of electronic components at this scale paves the way for “smart textiles” – garments that can alter their appearance or behavior based on environmental triggers.
Pushing the boundaries of color and visual effects, photonic nanostructures could transform fashion. Instead of relying on dyes, textiles could exhibit dynamic color-shifting effects based on their nano-engineered structure. Manipulating these structural colors could create remarkably vibrant and durable designs, providing an alternative to the fast-fading nature of traditional dyes.
This nanoscale control enables highly complex repeating patterns that previously seemed impossible, allowing fashion designers to envision entirely new garment construction methods. It also provides a potential solution to the inherent challenges of textile physics, allowing us to create garments that are simultaneously lightweight and warm by employing nanomaterials that enhance thermal properties while minimizing fabric weight.
This shift towards nanoscale design encourages a more experimental approach among fashion designers. Rapid prototyping and iteration are now easily achievable, allowing designers to rapidly explore innovative ideas and refine designs with minimal material waste. This ability to iterate quickly and efficiently holds significant potential for pushing the boundaries of aesthetic and functional integration. Combining computational design software with nanoscale printing technology could create textiles that elegantly balance form and function—optimizing the aesthetics and performance of each intricate pattern, paving the way for truly innovative and high-performance garments.
Micro 3D Printing Revolutionizing Precision Fashion Manufacturing in 2024 - On-Demand Production Reduces Fashion Industry Waste
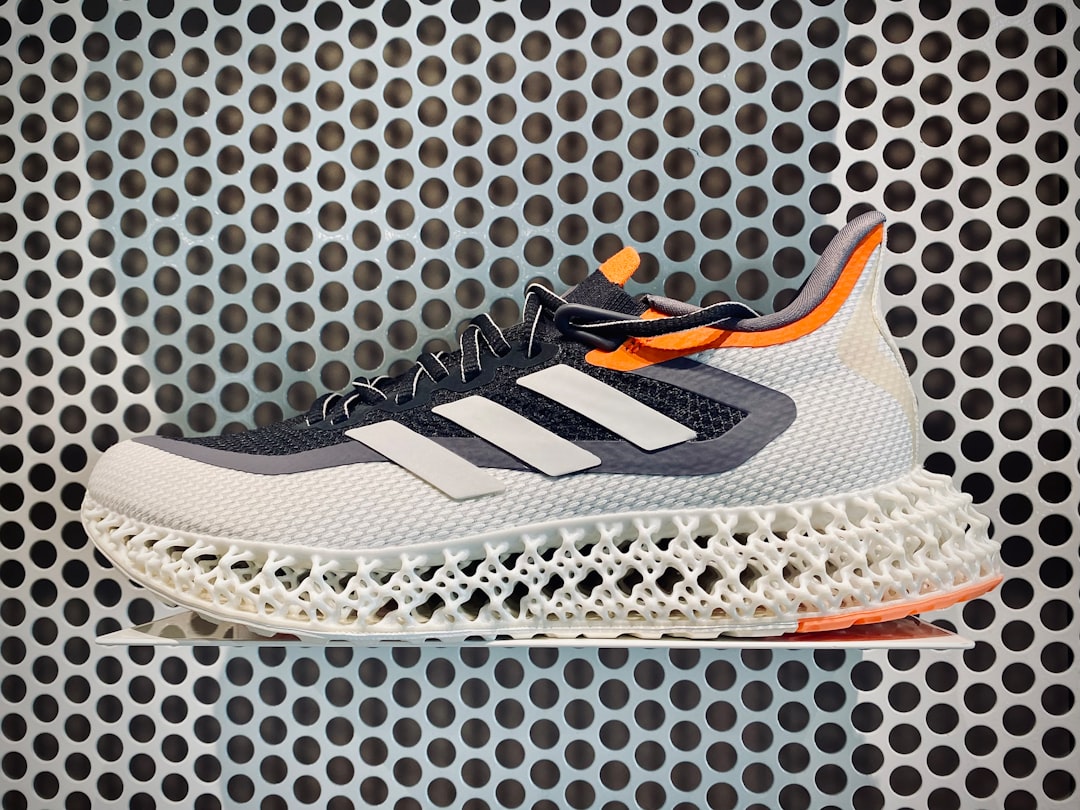
The fashion industry's shift towards on-demand production is a promising development in tackling the issue of textile waste. By producing garments only when they are ordered, this approach eliminates the need for large-scale manufacturing and subsequent excess inventory. This method reduces fabric waste dramatically as individual garments are created without the need for large-scale cutting and sewing that results in considerable scraps. This method also allows for a more customer-centric approach, reducing reliance on forecasting models that often lead to overproduction and subsequent waste. Companies are employing advanced technologies like micro 3D printing to enable this transition, with innovators like Unspun leading the way in developing automated processes for smaller, on-demand production runs. The ultimate goal is to create a more sustainable fashion industry through streamlined manufacturing that minimizes waste and resource consumption. While the transition may have its challenges, the potential for a more sustainable and ethical fashion future through on-demand production is undeniable. The increasing availability of microfactories and the growing interest in localized production further strengthen the potential for a more responsive, tailored, and environmentally-friendly fashion landscape.
Producing garments only when they're ordered significantly minimizes waste within the fashion industry. This "on-demand" approach eliminates the need to create vast quantities of clothes in advance, thereby reducing the mountains of leftover fabric and discarded scraps that are commonplace in traditional manufacturing. We are seeing early adopters like Unspun, Silana, and Pattern Project spearheading this shift, using advanced tools like microbatch 3D weaving and robotic garment assembly to achieve precision in fashion manufacturing. Unspun's Vega, a 3D weaving technology, is a great example of how just-in-time production can lessen the issue of unsold inventory and waste.
The vision is to deploy small, automated "microfactories" worldwide, essentially transforming how garments are produced. By only creating items after a purchase, this strategy sidesteps the unreliable forecasting methods that fuel overproduction. There is hope that this trend toward on-demand production can be a powerful force in establishing more sustainable practices within the fashion world. 3D printing's ability to reduce the enormous carbon footprint linked to excessive stockpiling is a key aspect of this emerging model.
Startups are actively working to develop these small-scale, highly automated microfactories, with the aim of mitigating fashion's environmental impact. The fusion of AI and 3D technologies in on-demand fashion is a transformative development, paving the way for more personalized and eco-conscious clothing.
These methods tackle critical challenges in the industry, including ethical considerations, the urgent need to decrease waste, and the difficulties of managing inventory effectively. Essentially, on-demand production streamlines the creation process. By marrying cutting-edge technologies with sustainable practices, we inch closer to a future where fashion can have minimal, if any, waste. While the shift to on-demand is encouraging, its implementation across the broader fashion world may encounter hurdles and require a more profound change in both consumer behaviors and industry practices to reach its full potential.
Micro 3D Printing Revolutionizing Precision Fashion Manufacturing in 2024 - AI-Driven Customization Reshapes Clothing Manufacturing
AI is fundamentally altering how clothing is made, allowing brands to create garments tailored specifically to individual customer requests. This shift towards made-to-order fashion is significantly empowered by technologies like micro 3D printing, which lets designers craft increasingly intricate and detailed designs while also promoting more sustainable manufacturing processes. As the industry moves towards on-demand production, the traditional reliance on mass production is lessening, highlighting a growing consumer desire for clothing that reflects their unique tastes. This transition not only caters to the demand for personalized apparel but also helps the industry grapple with the critical issue of textile waste, a major concern in traditional fashion production. AI plays a crucial role in this transformation by streamlining the design process and inspiring creativity, which leads to a more dynamic and responsive fashion landscape. It remains to be seen how successful the shift to AI-driven customized clothing will be in the long term but it presents exciting possibilities for the future of the fashion industry.
AI is increasingly influencing fashion design, particularly through software integration. Designers can now explore a vast array of design options within specialized programs, rapidly identifying trends and gauging consumer preferences. This capability accelerates the design process in a way that was previously unimaginable. It's fascinating how neural networks are being employed to translate simple sketches into detailed, rendered garment designs, complete with textures and color palettes. This technology has the potential to significantly streamline the initial stages of design, where ideas are first explored and brought to life.
Furthermore, AI-driven tools are enabling a deeper understanding of consumer behavior. By analyzing purchasing history and online interactions, brands can refine their collections to target specific demographics more effectively. This alignment of production with consumer demands is a noteworthy development, potentially reducing the risk of producing unwanted designs. It's also encouraging to see how AI is empowering consumers with customization options. Tools that allow shoppers to modify clothing elements—color, patterns, or fit—before making a purchase, could significantly enhance the shopping experience and potentially lower the number of returns due to fit-related issues.
AI is also impacting the way designers interact with materials. Simulation tools now allow designers to visualize how fabrics drape on virtual models, removing some of the uncertainty associated with material selection and leading to more confident design decisions. Beyond design, AI's influence extends to production processes. Genetic algorithms can now optimize fabric cutting patterns, leading to more efficient material utilization. This “marker making” process can minimize textile waste, a significant concern in fashion.
But AI's impact goes further than just design and production. AI is enabling the prediction of fabric behaviors, creating opportunities to explore new textile combinations with potentially novel textures and performance characteristics. This could reshape the materials we use in fashion, paving the way for more innovative and functional clothing. This capability to experiment with materials and optimize garment structures pushes traditional fashion boundaries, enabling new silhouettes and aesthetics that were once impossible to achieve. AI's role in analyzing massive datasets related to online activity and sales trends offers brands real-time insights into emerging styles and trends, enabling a more agile response to market shifts.
It's quite intriguing that some manufacturers are starting to incorporate real-time consumer feedback loops into the design process. This iterative design approach allows brands to rapidly adapt to changing preferences and market trends. This capacity for quick adaptation could be a significant advantage in today's fast-moving fashion landscape, but it will be interesting to observe the long-term effects of this real-time feedback integration and whether it truly fosters a deeper connection between the designer, the brand, and the consumer. It seems we're in the midst of a pivotal moment, where AI's computational power is blending with human creativity, shaping the future of fashion design and manufacturing in exciting, albeit potentially challenging, ways.
Micro 3D Printing Revolutionizing Precision Fashion Manufacturing in 2024 - Microfactories Transform Local Fashion Production Landscape
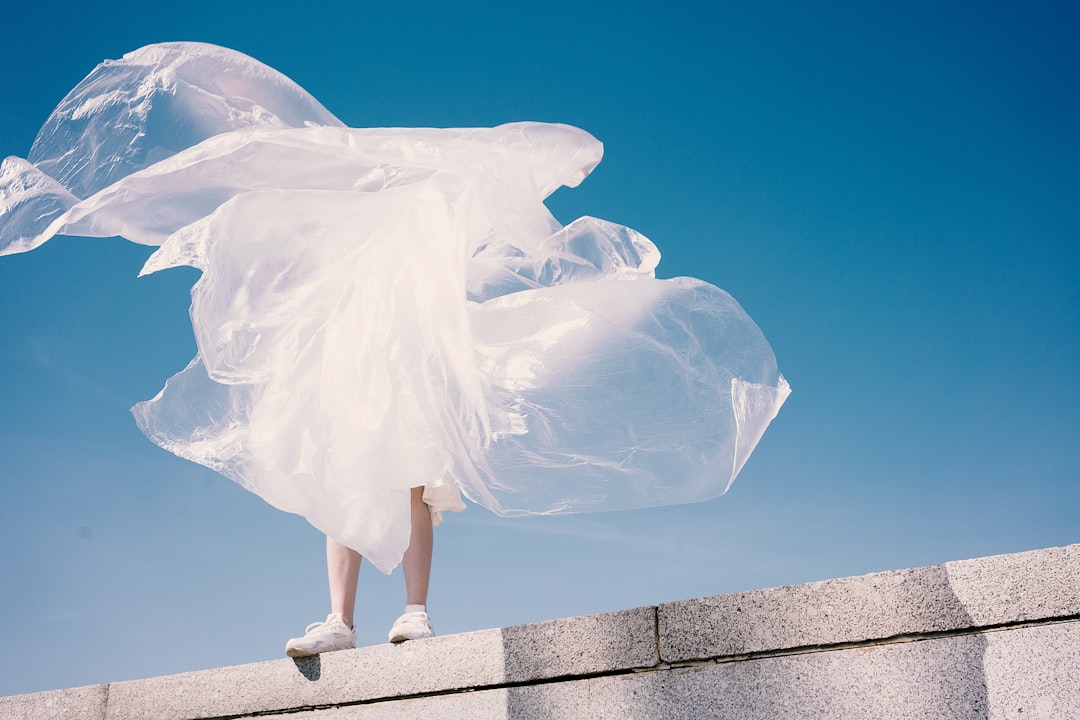
Microfactories are emerging as a key player in reshaping local fashion production, prioritizing on-demand and sustainable manufacturing practices. These smaller, modular facilities leverage advanced technologies, including micro 3D printing, to produce garments with reduced waste and a smaller environmental footprint compared to traditional approaches. By bringing manufacturing closer to consumers, microfactories enable faster production cycles and provide opportunities for more personalized clothing options. This localized production model not only diminishes the environmental impact associated with traditional globalized manufacturing processes but also empowers designers to experiment with novel materials and designs, leading to a more responsive fashion industry that's better equipped to adapt to evolving trends and consumer tastes. While the transition to this model may face challenges, it represents a potential path towards a more dynamic and eco-conscious fashion industry that places equal emphasis on design innovation and environmental stewardship. There are concerns that microfactories, while innovative, could increase the use of fossil fuels for energy and possibly other forms of pollution if not developed in a thoughtful manner. Additionally, some argue that microfactories could contribute to a further polarization in the fashion industry, creating a divide between the technologically advanced and those with less access to these technologies. Nonetheless, their emergence promises a more flexible and sustainable future for the fashion industry, though this is not guaranteed and many challenges still need to be solved.
Small-scale, modular manufacturing facilities, often referred to as microfactories, are fundamentally altering how fashion is produced at a local level. These facilities integrate advanced technologies, like AI, to streamline the manufacturing process and offer a localized alternative to traditional, often offshore, production methods. One of the key benefits is their ability to reduce the environmental impact of garment production, in part because they can produce garments on demand, effectively minimizing textile waste and eliminating the need for massive stockpiles of fabric. Interestingly, many of these facilities are designed to be waterless, which further contributes to their eco-friendliness.
A crucial element for success in these microfactories is the incorporation of sophisticated software and manufacturing equipment. This allows for flexible and adaptable production, a stark contrast to the rigid processes of conventional fashion manufacturing. We're starting to see collaborations, such as the one involving Kornit, Zund, and Fashion Enter, that highlight the potential of microfactories to revolutionize on-demand garment creation, ultimately aiming for a more sustainable future for the fashion industry. This movement is part of a broader trend towards digital innovation, often aligned with Industry 4.0 principles, that is transforming numerous manufacturing sectors.
The increasing adoption of microfactories may lead to a fashion industry that is much more responsive to consumers. This means greater customization options for customers, allowing for unique designs that meet specific preferences. As these facilities become more prevalent, the fashion production landscape will likely shift from mass-produced garments to more individually tailored pieces. The potential for localized workforce empowerment is another aspect to consider, as microfactories create employment opportunities within communities. However, we need to consider how the transition to this model impacts the traditional manufacturing sectors and labor practices. This shift presents a unique set of challenges as we work towards a more customized and sustainable fashion landscape. This is a fascinating period in the development of fashion manufacturing, and it will be interesting to see how the microfactory model continues to evolve and shape the future of design and garment creation.
Micro 3D Printing Revolutionizing Precision Fashion Manufacturing in 2024 - Cross-Industry Applications Fuel Fashion Innovation
The fashion industry is experiencing a surge in innovation fueled by the cross-pollination of ideas and technologies from other sectors. This is evident in the increasing adoption of micro 3D printing and other advanced manufacturing processes. These advancements are allowing for highly personalized, on-demand fashion production, aligning with the growing consumer desire for unique clothing. Simultaneously, this shift towards customized garments helps address the critical issue of textile waste inherent in traditional fashion practices. The ability to create intricate designs and incorporate functional materials into garments offers exciting possibilities, pushing the boundaries of not just aesthetics but also performance. Fashion's embrace of these innovations from other fields suggests a future where production methods will become more localized, resource-efficient, and environmentally conscious. This transition fosters new opportunities for creative design and promotes a more responsible and adaptable fashion industry, shaping a future where fashion is both innovative and sustainable. While the path forward may hold challenges, it undeniably showcases the potential for a more responsive and ethical fashion landscape.
The fashion industry is experiencing a fascinating surge of innovation fueled by cross-industry collaborations and technological advancements. We're witnessing a trend where ideas and techniques from seemingly unrelated sectors, like aerospace or medical device manufacturing, are finding unexpected applications in fashion design. For example, lightweight and incredibly strong composite materials initially used in airplanes are now being explored for creating high-performance garments.
Furthermore, the computational design space is seeing increased usage in fashion. Generative algorithms, inspired by natural structures (biomimicry), are being utilized to create unique and highly efficient patterns and shapes for fabrics. It's intriguing how these algorithms can draw inspiration from things like leaf veins or animal scales, potentially leading to garments with completely novel properties.
This cross-pollination of technologies extends beyond materials. Micro 3D printing, with its incredible detail and precision, enables designers to create intricate and complex textile structures that would be almost impossible to achieve with traditional techniques. Imagine garments with intricate lattice patterns printed directly into the fabric, adding both aesthetic appeal and functional benefits.
The fashion world is also exploring technologies originally developed for different purposes. Robotic systems initially employed in automotive manufacturing are now being used to offer unprecedented levels of customization, tailoring garments to individual body shapes and styles with amazing accuracy. This is especially evident in 3D printed clothing where each garment is truly unique.
This increased reliance on technology doesn't mean that traditional design processes are being abandoned. Instead, there is a powerful synergy developing between human creativity and software. Sophisticated computer-aided design (CAD) tools now readily integrate with 3D printing workflows, allowing for a smooth transition from initial sketches to a physical garment. This kind of streamlined process allows for more rapid exploration and experimentation, fostering a dynamic creative environment.
However, these technological advances also introduce new challenges. The rise of wearable electronics, embedding electronic circuits and sensors into garments to monitor biometrics, is a particularly intriguing development. It's still unclear how these components can be efficiently integrated into clothing while maintaining flexibility and comfort. Similarly, integrating temperature-responsive materials—such as phase change materials—into textiles raises questions about manufacturing scalability and overall design feasibility.
Additionally, fashion is embracing a new understanding of trends based on big data and AI. Designers are now able to react almost instantly to shifts in social media trends and consumer preferences. While this real-time feedback offers significant agility, it might lead to faster-paced and perhaps more ephemeral fashion trends.
Ultimately, this increasing reliance on interdisciplinary collaborations and technology is pushing fashion design towards a more holistic approach. Designers are now not only concerned with aesthetics but also with how materials interact with the wearer’s body and the surrounding environment. This means comfort, functionality, and environmental considerations are increasingly integrated into the design process. It's a fascinating transition, and it's exciting to observe how these cross-industry influences are reshaping the future of fashion.
More Posts from kahma.io: